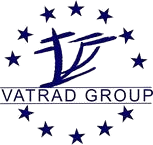
Galvanization Division
Galvanization Division include electro galvanized processes and hot dip galvanized processes.
The galvanizing process consists of three steps: surface preparation, galvanizing, and inspection.
Surface Preparation: For high quality hot-dip galvanizing, steel must be properly prepared prior to being immersed in a bath of molten zinc. During the surface preparation stage, material going through degreasing/caustic cleaning, pickling, and fluxing.
Degreasing/Caustic Cleaning: A hot alkali solution, mild acidic bath, or biological cleaning bath removes contaminants from the steel such as dirt, grease and oil.
Pickling: To remove mill scale and iron oxides, the steel goes through a diluted solution of heated sulfuric acid or ambient hydrochloric acid.
Fluxing: Through the final surface preparation step, any remaining oxides are removed in a zinc ammonium chloride solution and a protective layer is deposited on the steel to prevent any further oxides from forming prior to galvanizing.
Galvanizing: Following surface preparation, the steel will be immersed in a bath of molten zinc. The zinc kettle contains at least 98% pure zinc and is maintained at a temperature between 815º-850º F (435º-455º C). While steel is immersed in the kettle, the zinc reacts with the iron in the steel to form a series of metallurgically bonded zinc-iron alloy layers with the final top layer 100% zinc.
Inspection: The inspection process of galvanized steel is fairly simple. Zinc will not react with unclean steel, therefore a visual inspection of the product will provide a good assessments of the quality of the coating. Tests for coating thickness and adherence to ASTM standards will also be performed.
