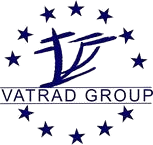
Surface Treatment Div.
In an effort to prevent corrosion or simply improve appearance, engineers will often specify an additional finishing treatment process for a portion, or all, of a metal part’s exterior surface after it has been machined or fabricated.
In addition, some of these surface treatments in the manufacturing process also provide enhanced mechanical or electrical properties that contribute to the overall functionality of the component.
The benefits of surface treatment
Improve appearance
Adjust the sizes
Add specific beautiful colors
Change the luster
Enhance chemical resistance
Increase wear resistance
Limit effects of corrosion
Reduce friction
Remove surface defects
Cleaning the parts
We provide the following metal surface treatment services
Anodizing (Anodized)
The function of anodizing is to form a thin layer of metal oxide on the outside of the parts. This layer of metal oxide can well enhance the corrosion resistance and wear resistance of the metal, and anodizing can add a beautiful appearance to the metal surface.
Plating (Electroplating)
The process of using an electric current to reduce dissolved metal cations so that they form a thin, coherent metal coating on the electrode to change the properties of the metal surface or add thickness to undersized parts. We often use chrome plating, nickel plating, etc.
Passivation
A common chemical finishing method, mostly used on steel and stainless steel, that uses a thin layer of protective material to form the outer shell to enhance corrosion resistance or reduce chemical reactivity. The passivation of stainless steel removes free iron and ferrous contaminants from metal surfaces with an acid solution to prevent rusting.
Black Oxide
Black oxide technology, also known as blackening or airbrushing, is a chemical process that creates a black conversion coating on stainless steel, copper and copper-based alloys, zinc, powdered metals, silver solder, and ferrous materials. Black Oxide coatings increase the corrosion resistance of part surfaces and minimize light reflections.
Painting
Painting is also a surface treatment process that increases the surface beauty of CNC machined parts and prevents corrosion or oxidation, but the protection ability of CNC machined parts is not as strong as the above surface treatment processes. It is a relatively comprehensive surface treatment process, but Painting can be done on any metal and non-metal parts.
Satin Finish
Some parts or materials have a matte finish because the surface has an uneven matte finish and a bright glossy finish, we want these satin metal finishes to be reflective, flat, and shiny, we need to use a satin finish , the visual effect of the satin-finished surface is related to the lighting of the part and the environment.
Polishing
Polishing is also known as polishing. Some parts have very rough surfaces when they are processed. If we want the surface of the part to have a smooth and shiny surface, then we need to rub the surface of the part or use chemical reactions. Produces a smooth, shiny surface that gives a specular reflection to the surface or reduces the diffuse reflection of the surface.
Abrasive Blasting (Sandblasting)
The role of sandblasting is to change the surface smoothness, or the surface roughness, and has a certain ability to beautify the surface. Abrasive blasting is the operation of using blasting equipment such as an air pressure system to propel a stream of abrasive material consisting of high-velocity sand grains into a metal surface under high pressure to remove surface contaminants, clean the metal, or add texture.
Powder Coating
Powder coating is very common, we see it in household appliances, aluminum profiles, automobiles, motorcycles, bicycle parts, most hardware accessories, and powder coating is the process of placing functional and decorative finishes (by electrostatic technology to applied as a free-flowing dry powder) and then cured in a heated environment, the powder coating creates a tougher finish than conventional coatings.
Conversion coating
Conversion coating, also known as chelate conversion, is used primarily as a corrosion inhibitor, to decorate finishes, or to maintain electrical conductivity. Conversion coating is the conversion of metals into protective layers through chemical or electrochemical processes.
